GROUP 31
Group 31 compact rotary actuators, models 31-M50 and 31-M30, include a single analog electronic control module which receives a 4–20 mA or 1–5 V dc input signal and provides a 4–20 mA or 1–5 V dc feedback for position control and indication.
AVAILABLE TORQUE AND TIMING COMBINATIONS FOR THE MODEL GROUP 31
Group 31 compact rotary actuators, models 31-M50 and 31-M30, include a single analog electronic control module which receives a 4–20 mA or 1–5 V dc input signal and provides a 4–20 mA or 1–5 V dc feedback for position control and indication.
- Electronic module has a deadband of 1.0% of span with sensitivity of 25% of deadband.
- The input signal span is nominally adjustable from 50% to 125% of the 4 V span, with the zero adjustable up to 120% of span, providing flexibility for split range operation.
Low Power Consumption
for Use with Uninterruptible
Power Supplies
The uniquely low power draw of Beck Group 31 drives permits the use of various standard uninterruptible power supplies for operationduring loss of AC power. Beck Sales Engineers can provide you with specifications on UPS equipment recommended for Beck drives.
Beck Group 31 drives equipped with feedback capability use a film potentiometer incorporated into the control module.
All modulating models feature electronic position indication. Direct AC models allow controllers to monitor drive position as the controller output directly positions the drive. Analog control modulating models provide electronic signal receiver circuitry, which compares the position indication to the control loop demand signal and provides automatic control.
DUAL FEEDBACK CAPABILITY
Models 31-M50, 31-M30, 31-350, and 31-330 have dual feedback capability, permitting user choice of 2-wire or 4-wire field connection.
Connections for feedback selection are made in the field and need not be specified on order.
Group 31 compact rotary actuator control modules include four cam-operated switches. Two switches open the motor circuit and function as end-of-travel limit switches, and two auxiliary switches are for external signaling as required by the user. The switch cams are driven directly by the drive’s output shaft for accurate control.
HOLDS POSITION UPON LOSS OF AC POWER
All Group 31 drives stay in place on loss of AC power, with a minimum holding capacity of 150% of rated drive torque. When power is restored, the drive automatically responds to control signal input to move to the position specified.
Convenient Local Operation – Included in the Analog Modulating models is an integral electric Handswitch, which permits safe, local operation at the valve’s individual location. This feature saves time during installation and allows adjustments to be made quickly and easily.
LARGE TERMINAL BLOCK FOR EASY FIELD WIRING
The upper board on the Group 31 drive provides wiring terminals for field connection. This board is easily accessible to minimize time needed for installation wiring and testing.
Beck’s Group 31 compact rotary actuators incorporate an exclusive no burnout motor, so that on-line dependability of valves is ensured. Heat-treated alloy steel and ductile iron hypocycloidal gearing transmits torque smoothly and powerfully to the output shaft. The Beck-built control motor provides millisecond response to signal commands in a modulating control loop—eliminating the coasting and overshooting problems typical of outdated electric actuators.
The motor stator of the Group 31 drive is molded into the centerpiece, providing stable delivery of torque without overheating and without burning out.
MECHANICAL STOPS PROTECTION FROM OVERTRAVEL DAMAGE
Rugged mechanical stops are furnished as a standard component of the valve mounting assembly. These stops prevent over-travel damage to valves and limit drive travel during manual cycling to maintain proper orientation of the drive output shaft with respect to switches and controls. A built-in position indicator shows the valve position.
MANUAL HANDWHEEL FOR CONVENIENT LOCAL OPERATION
A manual Handwheel is standard on all Group 31 models for use during installation and testing, or during power outages. This Handwheel does not require a declutch mechanism for operation and does not rotate during automatic operation.
CONTROL OPTIONS
Group 31 Compact Rotary actuators have one of several model numbers. Each of these Group 31 model numbers is equipped with an electronics package, which are called control options. While other Beck actuator products append the control option to the model number, the Group 31 product line has an inherent association between model number and control option that does not change. The control option number for Group 31 actuators is simply a reference to determine appropriate parts for maintenance. A basic description for each control option is provided below. For details on the electronics components, please visit the Group 31 Electronics section.OPTION
31-M30
DESCRIPTION
The standard modulating drive offering, models 31-M50 and 31-M30 are equipped with control option 3 electronics. Control option 3 electronics have an analog control board that may be controlled with a 4-20 mA or 1-5Vdc signal and provide an integral 4-20 mA or 1-5 Vdc position feedback signal. The position feedback signal may be of the 2-wire variety if specified at the time of order. Option 3 units are equipped with an electric handswitch for manual electric operation as well as stall protection with annunciation.
OPTION
31-330
DESCRIPTION
The control option 2 drive, consisting of model numbers 31-350 and 31-330, is a modulating unit controlled with 120 VAC direct to the motor. These units provide an integral 4-20 mA or 1-5 Vdc position feedback signal that is configured for a 4-wire setup, but may be of the 2-wire variety if specified at the time of order. When the drive hits the limit switch at either of the two end-of-travel positions, power is cut to the motor.
OPTION
31-230
Output Torque and Timing
MODEL # |
TORQUE (LB-FT) |
STROKE TIME (SEC./90°) (60 HZ) |
STROKE TIME (SEC./90°) (50 HZ) |
31-M50, 31-350, 31-250
|
30
|
24
|
29
|
31-M30, 31-330, 31-230
|
15
|
18
|
22
|
Specifications Common to All Models:
Drive Power | 120 Vac, single-phase, 50 or 60 Hz, 0.5A, 60 Watts |
Operating Conditions |
–40° to 65° C, (–40° to 150° F) 0 to 99% relative humidity |
Action on Loss of Power | Stays in place |
Handwheel | Provides manual operation without electrical power. Non-rotating during automatic operation, does not require declutching mechanism |
Motor | 120 V ac, single-phase, no burnout, noncoasting. Capable of 60 starts per minute |
Gear Train | Precision cut, heat-treated alloy steel and ductile iron. Self-locking and self-releasing, able to hold position at 150% rated torque |
Mechanical Stops | Prevent overtravel during automatic or manual operation. Mechanical stops are external to the drive |
Drive Net Weight | 25 lbs |
Max. Overhung Load | 500 lbs |
Switches
Cam controlled, field adjustable. Two limit switches (S3 & S4) open the motor circuit at end-of travel limits. Two auxiliary switches (S1 & S2) provied external signaling as specified through connections made at the terminal board. All four switches are SPDT and are rated for 1 amp at 120 V ac.
Enclosure
Precision machined aluminum alloy castings, painted with corrosion resistant polyurethane paint. All units meet NEMA 4 specifications and are also available FM approved for use in CLass 1, Div. 1, Group D; Class II, Div. 1, Groups E, F, & G; and Class III, Div.’s 1 & 2 hazardous locations.
SPECIFICATIONS FOR CONTROL OPTION 3 DRIVES (MODELS 31-M50 AND 31-M30): |
SPECIFICATIONS FOR CONTROL OPTION 2 DRIVES (MODELS 31-350 AND 31-330): |
|
Demand Input Signal Range | 4–20 mA OR 1–5 V dc | – |
Signal Span Adjust | 50% to 125% of 4 V span | – |
Signal Zero Adjust |
Up to 120% of span Split Signal Range: 4-12 mA or 12-20 mA |
– |
Deadband | 1% of span | – |
Sensitivity | 0.2% of span | – |
Feedback Signal * | 4–20 mA OR 1–5 V dc | 4–20 mA OR 1–5 V dc |
Output Stability for Temperature Change |
+/- 0.03%/°C of span for -40°C to 50°C | +/- 0.03%/°C of Span for -40°C to 50°C |
Stall Relay Contacts | Form A, 10 volt-amps at 120 V ac or dc | – |
Action on Loss of Input Signal (Power On) | Stays in place or runs to any preset position (configurable). | – |
Action on Stall | Relay contacts open after 68 seconds of stall, remote signal available. Power to motor is turned off. | – |
Handswitch | Permits local operation, independent of controller signal. The handswitch is located beneath the control module cover on the control board. | – |
HOW TO ORDER
The following instructions are provided to make it easy to specify Beck Group 31 drives. Complete wiring, operation and maintenance manuals are furnished with every drive order to make it easy for you to obtain an efficient, long-lasting installation.
Beck Sales Engineers are available to assist you in sizing drives for your applications.
- Basic model number
- Torque (lb-ft)
- Timing (sec./90°)
Using the information above, fill out the full model number according to the following formula:
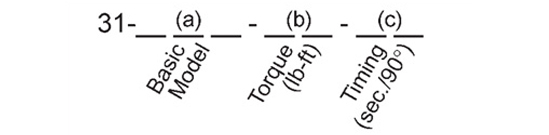
- Desired control input signal (Models 31-M30 and 31-M50 only)
- Desired power supply: 120 V, 60 or 50 Hz.
- Direction of control drive output shaft travel (CW or CCW, looking at the output shaft) desired with increasing signal (the resulting rotation for direct-coupled valves will be opposite that of the drive).
- Desired mounting option (A, B, C or D from the outline dimension drawing).